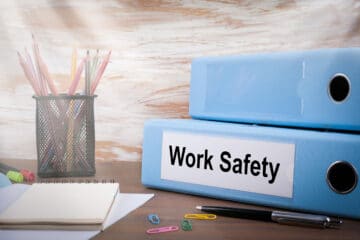
Written Safety Programs – Does Your Business Need One?
Author: Jeremy Wherren, CSP, CHMM, CMQ/OE – EHS Management Practice Leader
With all of the responsibilities required to run a business, it can be difficult to think about (let alone implement) a written health and safety program that addresses all of the applicable Occupational Safety and Health Administration (OSHA) requirements relevant to your industry. Or, worse yet, an employee filed a complaint and an OSHA inspector has just shown up in the lobby requesting to conduct an inspection of your facility. Are you ready? Do you know what’s required of you to maintain compliance?
Even if your company checks all of the boxes when it comes to performing work safely and conducting training for your employees, do you have the necessary written programs in place to help maintain compliance? OSHA regulations are ever-changing: whether by revision of existing requirements or publication of brand-new regulations, and it can be difficult and overwhelming to both understand and keep up with exactly what’s required for your business.
The OSHA website summarizes the following standards requiring a written program, which are commonly applicable to businesses depending on their operation. Does your company meet any of these standards?
- Hazard Communication – If employees may have exposure to chemicals in the workplace – OSHA 29 CFR General Industry Regulation 1910.1200
- Emergency Action Plan – If your facility has more than 10 employees – OSHA 29 CFR General Industry Regulation 1910.38
- Fire Prevention Plan – If your facility has more than 10 employees – OSHA 29 CFR General Industry Regulation 1910.39
- Control of Hazardous Energy (Lock Out-Tag Out) – If your employees service or maintain machines or equipment that could start up unexpectedly or release hazardous energy – OSHA 29 CFR General Industry Regulation 1910.147
- Personal Protective Equipment (PPE) – Employers must perform an assessment of each operation in their workplace to determine if their employees are required to wear PPE – OSHA 29 CFR General Industry Regulation 1910.132
- Respiratory Protection – If employees are required under the regulation to wear a respirator – OSHA 29 CFR General Industry Regulation 1910.134
- Hearing Conservation – If employees are exposed to excessive noise > 85 decibels (rule of thumb: conditions that make normal conversation difficult) – OSHA 29 CFR General Industry Regulation 1910.95
- Bloodborne Pathogens – If employees may be exposed to blood or bodily fluids as part of their assigned duties – OSHA 29 CFR General Industry Regulation 1910.1030
This list is by no means all-inclusive, and some industries have additional written program requirements, such as construction under 29 CFR 1926. And it’s not just federal OSHA regulations that need to be verified for business – there are 22 states with their own OSHA-approved plans that cover both private and local government workers, and another 6 states with plans that cover just local government workers (the remaining states are covered by federal OSHA).
Several states also have their own specific requirements for health and safety related programs, which may or may not be under an OSHA-approved plan. For example, the New Hampshire Department of Labor requires a Joint Loss Management Committee or “safety committee” in a workplace with more than 15 employees, as well as a written safety program with specific elements.
Employee safety is a genuine priority for any business leader worth their salt, but even the most well-intentioned owners and professionals may not know what they don’t know. A qualified Environmental, Health, and Safety (EHS) consultant can provide guidance and understanding to businesses considering the applicability of EHS programs within their operations. An investment in a written health and safety plan is an investment in your employees, your clients, and your business. And often, as the saying goes, “what gets written down, gets done”.