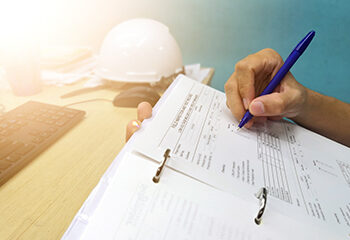
By Alyssa Epstein, Project Scientist
A Phase I Environmental Site Assessment (ESA) is the first step in completing environmental due diligence on a prospective property and is generally completed prior to purchase or refinancing. Sometimes this assessment is required by a bank to protect their investment prior to issuing a loan.
The standards for a Phase I ESA are established by the American Society for Testing and Materials (ASTM). The assessment includes review of Federal, State, and local databases and records, a site inspection, and interviews with owners, occupants, neighbors, and/or local government officials to identify if any environmental liability from existing contamination or a potential release of contaminants exists at the Site. These would be considered recognized environmental conditions (RECs).
Results of the Phase I ESA drive future environmental assessments. No further assessment is required if insignificant or no RECs are identified; however, an ASTM Phase II investigation would be warranted if significant RECs are present. The Phase II includes intrusive investigations such as advancement of soil borings to install monitoring wells and evaluate subsurface conditions, laboratory testing of soil and groundwater samples to determine actual levels of contamination, and/or geophysical testing (ground penetrating radar, metal detector, etc.) to identify subsurface structures (i.e. underground storage tanks or vaults) that may be sources for contamination.
Analytical testing – Pros and Cons
Analytical testing should be tailored to site-specific RECs to determine which compounds to include for analysis. Laboratory results will help further determine liability due to environmental conditions by quantifying levels of specific contaminants; however, know that specific compound concentrations may trigger additional site investigations, remedial action requirements, and involvement by the State regulatory agencies. This is often a Catch-22, as the buyer often wants to know exactly what they’re getting into, but the seller doesn’t want to be open to additional risk/remediation costs should the sale not go through. It’s not uncommon for the seller to limit Phase II investigations including laboratory testing since State-agency involvement often REQUIRES additional and costly remediation and navigation through the state regulations and sometimes the presence of contamination devalues the property (although this is not as common as it was 10 or 20 years ago). Be sure to work with your environmental professional to help leverage the appropriate level of pre-sale investigations that helps both protect you and moves the sale forward.
Additional Considerations – Site Buildings
Aside from potential soil and groundwater contamination, hazardous building materials may be present within building materials; therefore, a hazardous building materials survey (HBMS) may be warranted if a property already has a building. Municipalities often require an HBMS prior to issuing a demolition or renovation permit, so performance of an HBMS should be considered prior to site redevelopment if major changes to the building structure is planned.
The HBMS will locate and quantify hazardous materials within the building envelope. These typically include asbestos containing materials (ACM), lead-based paint (LBP), polychlorinated biphenyls (PCBs), mercury, mold, and other universal wastes present in the building(s). The intent of the HBMS is to identify materials where regulations prescribe specific handling and disposal requirements to protect human and environmental health. Abatement and removal of these materials can be costly; therefore, results of the HBMS may affect overall project budget and influence sale price.
Often materials included in the HBMS are misunderstood. Here are some common misconceptions for materials typically identified:
- Asbestos was widely used in building materials from the early 1900s to 1978, and it was used in many more products than the typical pipe or boiler insulation most people associate with asbestos. Suspect materials include wall board, floor tile, caulking, roofing materials, joint compound, and even plaster. Due to health effects, asbestos was prohibited via a series of bans that culminated in 1978, although use of specific asbestos products is still permitted even today. Because of this, there is no exemption for an asbestos survey due to building age.
- PCBs were banned from production in 1979; however, until then they were commonly used in hydraulic and dielectric oils and fluids found in transformers, garage lifts, and fluorescent light ballast. In addition, PCBS were added to building materials such as caulking to serve as a plasticizer to keep the material soft and flexible and to paint to provide resiliency in wet applications (such as wet wells, pump houses, and even swimming pools). There are no regulations that obligate to test for PCBs; however, the handling and disposal of PCB containing materials are regulated by EPA. This catch-all often prompts testing for PCBs to adequately characterize the waste stream. Toxic Substances Control Act (TSCA) regulations require abatement of PCB containing materials if PCBs are detected above certain thresholds, so Nobis recommends testing for PCBs only if you are certain the project will move forward (we generally avoid PCB testing during a feasibility study but promote it prior to developing design documents/specifications).
- LBP abatement requirements are dictated by the reuse scenario. The presence of LBP is much more regulated in residential structures. Lead screening results are not only used to assess lead levels for proper material handling and disposal, they are also used to calculate worker exposure levels for Occupational Safety and Health Administration (OSHA) compliance. OSHA regulations typically dictate lead handling procedures since their regulations mandate safe handling of materials that contain any level of lead greater than 0.0 mg/cm2 (vs EPA and the Department of Housing and Urban Developments (HUD) regulations that identify LBP as a material that contains lead equal to or greater than 1.0 mg/cm2). Note that most pre-demolition/renovation lead surveys do not meet HUD requirements for a residential use scenario.
- It’s obvious that chemicals stored in the building (paints, cleaners, etc.) need proper handling and disposal, but other universal wastes and regulated materials such as mercury containing components (switches and fluorescent light bulbs), battery-powered components (emergency lights, exit signs, and alarm systems), and even water fountains and computer monitors may require special handling and disposal prior to renovation/demolition.
The presence of environmental contamination and hazardous building materials can add significant cost to your site development or renovation project. Due diligence and proper pre-characterization can help limit liability and costly change orders, and pre-planning can help keep a project on schedule.