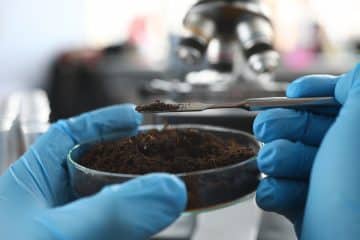
Contaminated Soil Management in Massachusetts – Plan Ahead and Plan Carefully!
Author: Jeffrey Brunelle, CPG – Director of Project Development
In Massachusetts, it’s becoming increasingly challenging to manage excess soil generated during construction that requires off-site disposal. Today, there are fewer facilities that will accept soil for disposal within the Commonwealth. Contaminated material exceeding the Reportable Concentrations as promulgated by the Massachusetts Department of Environmental Protection (MassDEP) typically must be disposed out of state.
Disposal restrictions and increasing costs often have big impacts on the overall project budget and schedule, so early soil management planning is imperative to the smooth execution of a construction project that includes earthwork and off-site soil disposal.
Plan for Soil Management
It’s important that consultants explain and educate their clients early on that soil disposal is complex and that contamination can be encountered even on supposedly clean sites. Often clients don’t include soil disposal in the budget, as they may assume sites with no evidence of historical contamination to be clean; however, even assumed clean sites may still have stringent disposal requirements.
It’s very rare to have soil, especially from urban sites, that is deemed to be acceptable for unrestricted use. Even marginally contaminated soil or soil with compound concentrations less than MassDEP reportable concentrations require some special handling and disposal to ensure that contamination is not inadvertently spread to a new location.
Soil characterization and disposal costs can very easily and quickly grow significantly, depending on the volume of soil and compounds encountered in the soil. And it’s through effective soil management planning that one can best avoid costly change orders or unplanned costs related to soil management and disposal.
Soil Testing
Soil to be moved off-site needs to be sampled for a robust analytical suite to identify reuse and disposal options. The number of samples to be collected depends on the volume of soil to be disposed and the permit requirements of the licensed disposal facility. In addition, facilities may also have specific acceptance criteria outside of analytical testing, such as requirements for soil field screening using an Photoionization Detector (PID) or observation of soil excavation by a certified environmental professional.
Analytical data will be compared to disposal facility acceptance criteria to establish available off-site disposal options. Facility acceptance criteria varies from facility to facility and is based on the facility’s operating permit. Permit requirements are often based on a facility’s processes and location.
There’s Liability with Testing
Whenever you collect analytical samples, results are subject to comparison to the MassDEP standards promulgated in the Massachusetts Contingency Plan (MCP). Data that exceeds the MCP Reportable Concentrations requires MassDEP notification and contaminant remediation under the MCP.
Projects tracked by MassDEP under the MCP can be costly and time consuming. Be sure that your project plans warrant soil sampling prior to sample collection to limit potential cleanup liability under the MCP.
Think About Your Soil Management Options
Can soil be reused on-site? If so, soil sampling may not be warranted. Is in-situ soil characterization or stockpile profiling more appropriate for your project? Pre-characterization of in-situ soil can be helpful for budgeting purposes; however, this approach does not guarantee that pre-characterized soil is always representative of actual soil to be disposed. Characterization of stockpiled soil that has been excavated is always more representative, but unknown costs, schedule, and facility selection implications may be unknown until the time of sampling. Also, there’s not always adequate physical space on a jobsite to store and manage stockpiled soil.
These soil assessment management implications should be discussed with the project team early in the job process to find which method will work best for your project. Soil management plans should be documented within the project specifications and in a Soil Management Plan for unregulated sites or a Release Abatement Measure Plan (RAM Plan) if the Site is tracked under the MCP.
Acceptance for Disposal Takes Time
Analytical turnaround times are typically around two weeks due to the robust analytical suite mentioned above and due to the time required for sample analysis. Often analytical results cannot be rushed since some of the analytical processes take a set amount of time (such as extraction for Polychlorinated Biphenyls or metals).
Disposal facility selection may be dictated by the project schedule. There may not always be an earthwork contractor under contract to select disposal locations during the early project phase when soil management decisions are made, so it’s key to make clear upfront who is responsible for this task. Typically, it is the responsibility of the earthwork contractor to select disposal locations, and they are not always present in the project planning phase.
Typically, it is the responsibility of the earthwork contractor to select soil disposal locations; however, the contractor may not be under contract during the early project phase when soil management decisions are made. Facility selection may be dictated by the project schedule, so it’s key to decide upfront who is responsible for this task.
Soil profiles are required by each proposed disposal facility. As mentioned above, acceptance criteria vary from facility to facility. Because of this, facility evaluation can be complicated and take time. Also, the time needed for the disposal facility to review the soil profiles has to be taken into consideration. Often a disposal facility contracts with an environmental firm to review their disposal applications. Understandably, this further adds to the acceptance timeline. Also, if your site is regulated by the MassDEP and is subject to requirements of the MCP, a Licensed Site Professional (LSP) is required to complete the soil profiles and transportation paperwork.
Plan for a month or more for facility acceptance.
Disposal Options
Do some “what if” scenario planning, but always work toward the best disposal option and, again, start this effort early on. Have a contingency plan and back-up facilities for soil disposal. Obviously, as soil volumes and contamination increases, so do the associated disposal costs.
Soil with concentrations consistent with background levels (as defined in 310 CMR 40.0006) typically do not have reuse restrictions since contaminant concentrations are non-detect or extremely low. This type of soil may not generate a disposal cost, but may carry a liability due to potential human health concern risks, as reuse locations could include a school, daycare, or backyard.
Soil classified as hazardous waste carries a high cost of disposal due to the potentially toxic characteristics of this material and the specialized handling and disposal requirements. No in-state facilities are available for hazardous waste disposal, and transport to an applicable disposal facility could be as far as Ohio or Canada.
Unrestricted use and hazardous waste classifications “book end” the wide spectrum of soil management classification. Typically, soil is classified as either impacted soil or contaminated soil. Impacted soil contains compound concentrations greater than background levels, but less than the MCP release notification thresholds. Contaminated soil contains concentrations of contaminants that exceed in-state acceptance criteria and are not classified as a Hazardous Waste.
Impacted soils may be reused at in-state locations such as a MassDEP-permitted reclamation soil project under MassDEP Policy COMM-15-01 or reused as daily cover, intermediate cover, or pre-cap contouring material at in-state unlined or lined landfills under the MassDEP COMM 97 Policy.
COMM-15 facilities require scrutiny for acceptance since acceptance criteria is not universal. COMM-97 acceptance evaluations are easier because the acceptance criteria are universal, as published in the policy documents. Disposal at these in-state facilities can be problematic, as quantities to be accepted may be capped yearly and these facilities do not always operate on a fixed schedule. With varying schedules for operations, these facilities commonly stop accepting waste as they reach their established annual capacity, rendering these disposal options unreliable.
There are no longer any in-state options for disposal of contaminated material, making hauling and disposal costly under this soil category. Also, impacted soil may be managed as contaminated soil (and carry a higher premium as such) as disposal options for impacted soil become no longer available.
Consider Soil Reuse On-Site
Another option is to reuse soil that is not grossly contaminated on-site. MassDEP permits on-site soil reuse typically when contaminant concentrations do not pose a significant risk to human health and the environment and reuse of soil will not degrade the soil quality at the site.
The Similar Soils provision prohibits contaminated soil from being moved to a portion of the site that has lesser contaminant concentrations (i.e., a cleaner area of the site), so some site investigation may be necessary to document site conditions for reuse.
Another consideration for site reuse would be geotechnical suitability to ensure the material to be reused on-site meets construction requirements. This brings up a key point – soil contamination is not the only factor that may require off-site disposal. Soil with high debris components may be unusable in construction and therefore would require off-site characterization and disposal.
Conclusion
Soil management considerations as an afterthought are often costly to the project. Disposal costs may vary from as little as $22 per ton for COMM-15 soil to more than $450 per ton for hazardous waste. Remember that economic variables such as cost of fuel, personnel shortages, and supply chain issues each can adversely impact your disposal costs.
Ignoring or delaying soil management planning may result in hefty project change orders and significant project delays. Carry a monetary contingency for soil management evaluations and off-site soil disposal to avoid surprises. Also – your site is never as clean as you think it is. It’s likely going to cost something for off-site disposal of soil you can’t reuse on-site. So, plan ahead and plan carefully!